In the high-stakes world of motorsport, every component must withstand extreme forces and temperatures. To help cool these parts, conveyors are integrated into the bodywork or as appendages keeping the components within the optimal working range, ensuring performance, efficiency and durability of the system. With the advent of 3D printing, the possibilities for creating these complex parts quickly and efficiently have reached new heights.
3D printing is a perfect option for bringing these parts to fruition, as 3D printers can easily produce the complex, curved geometry needed, quickly and if necessary, repeatedly.
This is why the team of Angelo Di Gioia and Giovanni Di Franco used a Raise3D printer to successfully engineer a useful motorcycle braking system air cooling duct for the acclaimed KTM Duke 890 R.
The result is a 100% functional part designed and produced with extreme efficiency in terms of time and costs.
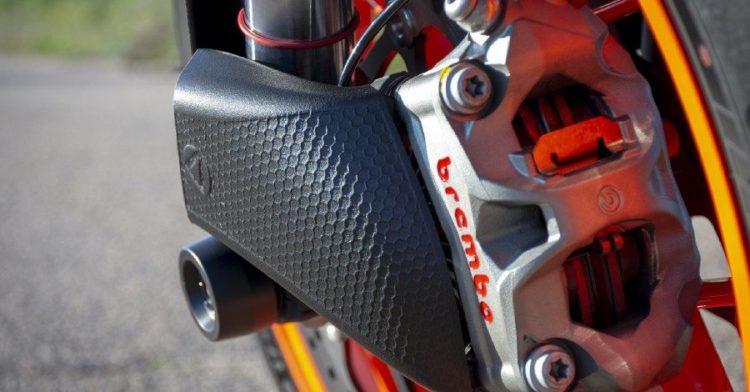
Raise3D printer successfully engineered a useful motorcycle braking system air cooling duct
Unlocking Unparalleled Design Efficiency
The first part of the process was to scan the motorbike, specifically the areas that needed cooling. Armed with a state-of-the-art3D scanner, they captured the precise information needed and seamlessly transferred it into cutting-edge modeling software. From here, the modeling of the new part can be carried out.
3D printing is compatible with most modeling software, as virtually all modeling software supports the export of models in 3D-printer-friendly formats, with the STL format being the most common choice.
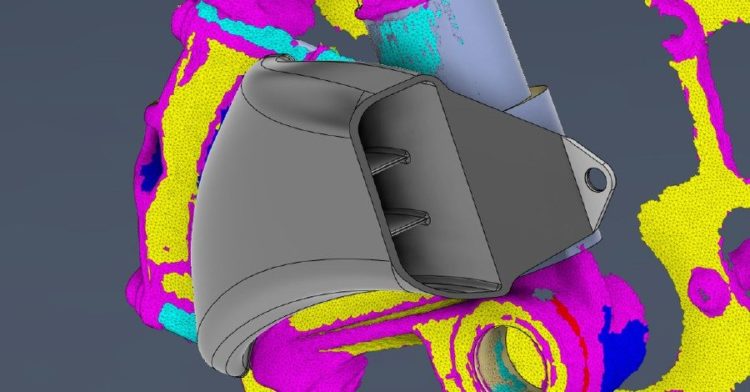
All of the modelling software can export the resulting models in formats compatible with 3D printing
Harnessing the Power of Fluid Dynamics Simulation
An important part of the process is to validate the effectiveness of the component using fluid dynamic analyses. Through meticulous refinement of the air duct’s geometry using advanced simulations, they achieved superior results even before physical prototyping.
Subsequent tests can be carried out on a test bench or a wind tunnel and then on test circuits with the parts actually on the motorbike. This is where the true advantage of 3D printing shines through. The ability to rapidly produce multiple iterations of the final part significantly reduced testing time, expediting the entire development process.
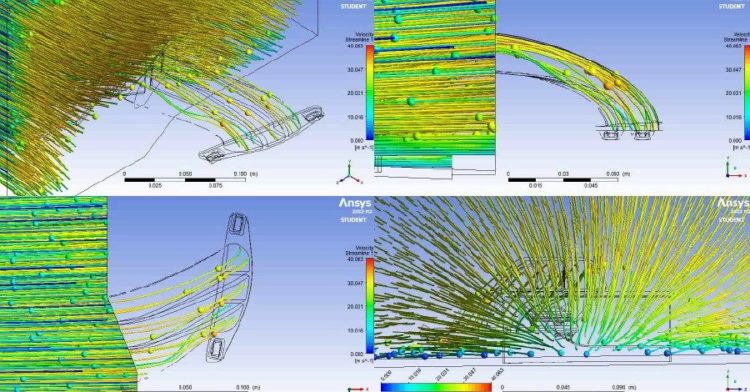
Multiple iterations of the final part can be quickly produced and applied to the bike
Excellent Performance from Today’s Thermoplastics
The advent of Fused Filament Fabrication (FFF)3D printing technology today allows the production of items made from a wide range of available thermoplastics, among which there are carbon fiber-reinforced filaments. Their resistance to impact from debris makes them the ideal choice for motorsport applications, while their superb resistance to water and chemicals ensures durability in outdoor environments plagued by rain and air pollution.
In addition, its excellent resistance to water and chemicals makes it a particularly suitable material for outdoor use that is resistant to rain and air pollution.
In their own words “High print resolution, reliability and precision are the winning ingredients for a high-performance product with an attractive design, and the Raise3D Pro3 3D printer is the ideal tool for small batch production of end-use parts.”
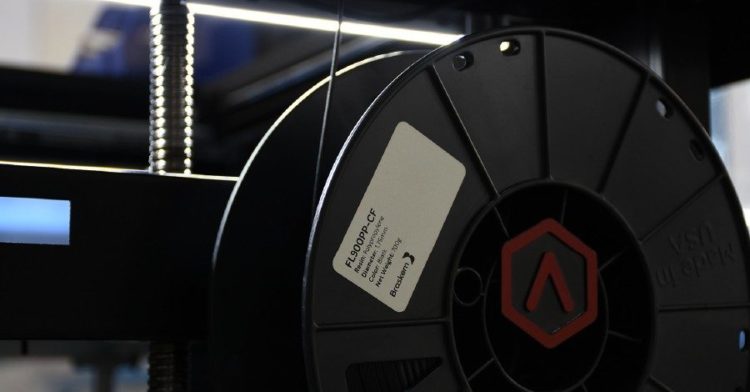
Raise3D Pro3 3D printer is the ideal tool for small batch production of end-use parts with carbon fiber-reinforced filaments
Customized Production at Your Fingertips
Another aspect that Angelo and Giovanni highlighted was the enormous ability to customize each and every part.
“Nothing is more tempting than a product that can be customized,” they said.
With the ability to effortlessly incorporate logos, textures, and other modifications, they could rapidly produce tailored parts to meet specific requirements. Some of this can be done using ideaMaker, Raise3D’s free slicing software. Apart from easily generating .gcode file, it can manage print queues thanks to the ability to monitor and control the printer wirelessly. It has a corresponding online library that is very advantageous to anyone who has a Raise3D printer.
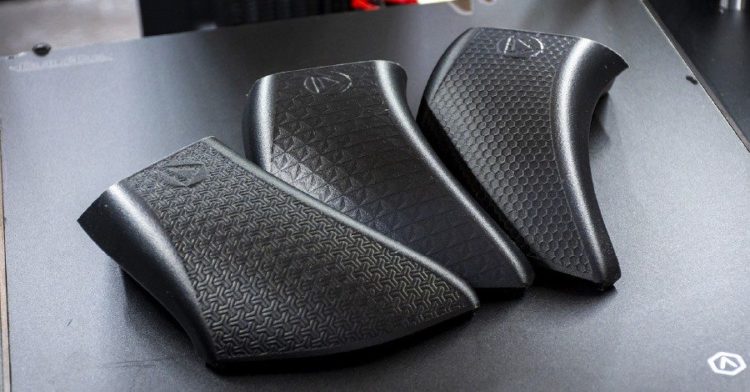
Logos, textures and other modifications can be added and produced very quickly with Raise3D’s Slicer – ideaMaker
Embrace the Future of Prototyping and Manufacturing
The various advantages can be summed up in their own words:
“Excluding the design and modeling time of the component, in a total of 16 hours it was possible to obtain the first conceptual prototype (scanning, post-processing and prototyping) with fully satisfactory results,” they said. “Furthermore, the cost applied by Fastparts for the production of the pair of conveyors is around €100, against a market value of these special components which can reach up to €300.”
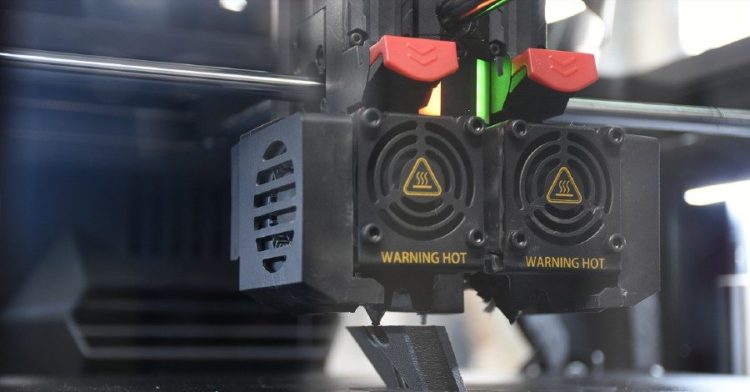
Time-saving and cost-efficient to obtain the prototype with satisfactory results
This story was brought to you by Crea3D, Raise3D’s reseller in Italy. You can read the full article here.