High-end industries, such as aerospace and automobile manufacturing, already make extensive use of 3D printing. However, this additive technology is finding more applications in other areas, such as beverage vending machines. Bettidrink is an environmentally-friendly start-up in Germany that manufactures and sells sustainable beverage supply solutions called Betti. Betti consumers receive a glass or plastic bottle and dispense the beverage they want from a Bettidrink vending machine on demand.
Bettidrink’s RnD team applied 3D printing technology to mass-produce customized parts used in beverage vending machines. The company partnered with Raise3D to improve printing efficiency and the quality of the fabricated parts. The comprehensive and high-performance package of 3D printing solutions provided by Raise3D proved to be able to meet the needs of continuous iterative design and end-use production.
Time-Consuming Traditional Manufacturing VS FFF 3D Printing
Bettidrink has long recognized that it is not cost-effective to manually construct a complex and irregular model using traditional production methods. Traditional production methods involved using subtractive manufacturing to make a mold. Subtractive manufacturing is when excess material removed from an original block of that material until the desired shape is achieved. This process uses a great quantity of material, which as a result increases cost, time spent, and waste. In addition, post-processing a mold is difficult, leading to increased material costs and production difficulties. Once the sample design is approved, Bettidrink needs to entrust a third-party company to make the mold. If the sample needs to be revised, the mold must be reproduced, lengthening the production cycle and doubling the cost.
3D printers can produce assembly-free and complex structures, and also signifies a reduction of production processes and costs while facilitating unlimited design iterations. With such advantages, the Bettidrink RnD team invested in 3D printers for parts production.
Bettidrink’s First Attempt at 3D Printing
In the beginning, Bettidrink encountered issues with the original 3D printers the RnD team purchased. First, the printers had a build volume that was not sufficient to accommodate the entire tray parts they designed, each being approximately 300x100x250 mm. Secondly, these 3D printers did not support 0.8mm nozzles, a size required to print this particular type of tray. Originally, Bettidrink had to print with regular-sized nozzles, and that led to an extended production time. However, Bettidrink found that when a 0.8mm nozzle was used to print a model, the printing time was greatly shortened and efficiency was maximized, without affecting the surface smoothness and geometric accuracy. Thirdly, these printers could not provide high-precision and highly smooth surface parts. Fourth, the printers did not support high-performance printing materials, such as PETG, and lacked advanced printing parameters and an ecosystem. All these issues led Bettidrink to find a more efficient and convenient 3D printer.
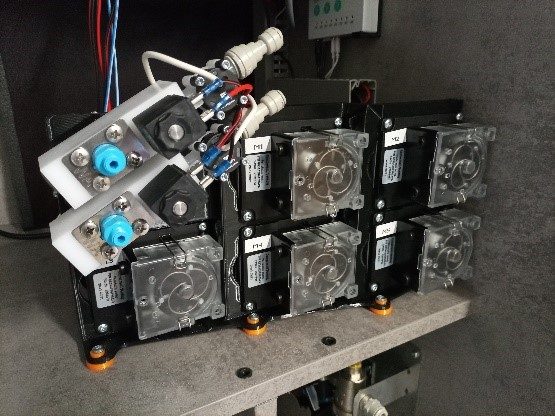
Trays printed by Raise3D Pro2 printers.
Bettidrink’s 3D Printing Results Using Raise3D Printers
Bettidrink partnered with Raise3D to invest in a 3D printer with a larger build volume, higher printing accuracy, a more stable internal structure, and a more supporting more varied 3D printing solutions. The Raise3D Pro2 dual extruder 3D printer provides a larger build size of 305×305×605 mm, which can fully meet the needs of Bettidrink to print larger trays. The printing accuracy of the Pro2 printer is within +/- 0.100 mm. This dual-extruder 3D printer is also equipped with a unique motion control system, meaning it can print complex structures flexibly and accurately. The Pro2 supports a range of nozzles, namely 0.2/ 0.6/ 0.4/ 0.8/ 1.0 mm diameters, so Bettidrink’s R&D team can replace the nozzles according to the projects’ needs.
The Pro2 dual extruder 3D printer supports a variety of environmentally friendly thermoplastic filaments. It is also compatible with filaments from other manufacturers. Bettidrink successfully used the Pro2 to print Extrudr’s PETG filaments. Raise3D launched the Open Filament Program (OFP) and has tested a variety of PETG filaments that are robust, and compliant with RoHS and Reach standards. Users can visit the OFP page to learn about the world’s major filament manufacturers and adaptable filaments participating in the OFP program.
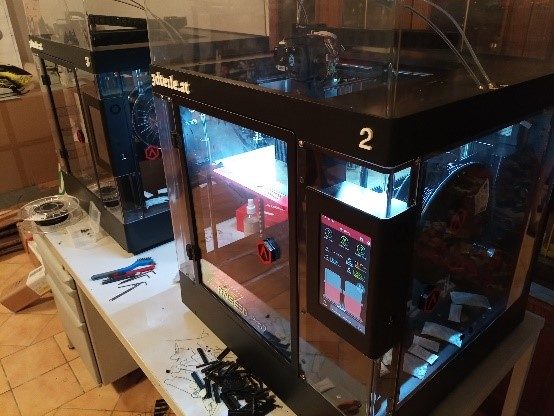
Bettidrink uses Pro2 Printer to greatly reduce the costs and enhance the product’s iterative design phase.
The Consistency, Reliability and Efficiency of the Pro2 Dual Extruder 3D Printer
The Bettidrink R&D team was surprised by the consistency, reliability, and efficiency of the Pro2 printer. Raise3D provides users with a coherent printing ecosystem from model slicing to printing. After designing and slicing the model, the R&D team can immediately upload the model to the Pro2 printer via the remote network and start printing. One Bettidrink engineer said, « There was no waiting time or time which goes to waste during the whole order process – it was simply sliced and printed on its own printer. »
The Pro2 printer reduces the time it takes to print and the cost of materials. The entire model production takes only 10-11 hours. The cost of printing this tray is much lower than the expense of making it with metal or other machined parts. Bettidrink’s engineers also stated that “there are no tool costs or other costs before manufacturing.”
Raise3D Allows for Less Limited Product Iteration Process
Bettidrink engineers admired the unlimited product iteration achieved after using the Pro2 printer. They stated that » Design revisions are always possible and there are no limitations for further development of the part. » Since the prototype is similar to the final product, it shortens the iterative process and the time to put the product into use. Work that used to take 10 days to complete can now be completed within a day with the Pro2 3D printer. Through simple post-processing, such as sanding, painting, and coating, engineers can present ultra-realistic prototypes for designers to review and modify within 24 hours.
The various thermoplastics filaments that Raise3D Pro2 can 3D-print are sufficient to meet their different needs. The R&D team of Bettidrink also uses various high-performance and highly adaptable composite filaments provided by the OFP project launched by Raise3D. The specially-developed slicing program, ideaMaker, also provides slicing parameters suitable for a variety of filaments, and the best model printing parameters can be obtained without any kind of manual adjustment. Raise3D helps Bettidrink break the obstacles they previously encountered in the process of model development and production.
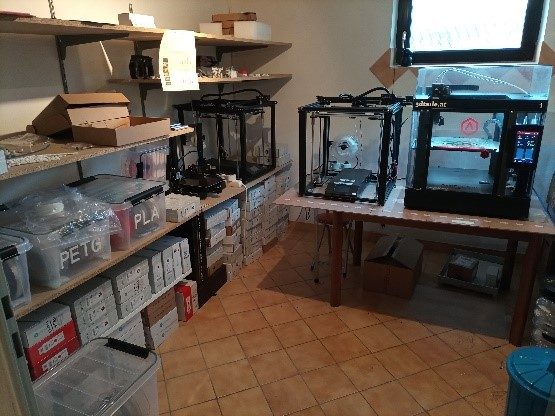
Bettidrink uses high-performance composite filaments provided by the OFP project.
3D Printing Is Seen on the Streets of Germany
The Raise3D Pro2 printer helps Bettidrink obtain the shortest design iteration process and the best final product in a cost-effective manner. In the future, Bettidrink will continue to use Raise3D Pro2 printers for iterative development and mass production of parts. Bettidrink will use vending machines that use Raise3D Pro2 printed parts to promote 3D printing technology on the streets of Germany.
This case is shared by OKM3D, which is Raise3D’s distributor in Germany.