Fashion trends change faster than ever before, and as a consequence, manufacturers are obliged to focus more on small-batch production. This trend and transition in production includes the sneaker-manufacturing industry. Almost every major shoe manufacturer is exploring different methods to achieve faster market times without having to face extraordinary tooling costs. While most current manufacturing methods are unable to meet the increasing demand for faster small-batch production, 3D printing is progressing towards fulfilling this need. In 2020, a few giants of the sneaker-manufacturing industry used Raise3D products to make production breakthroughs and achieve even more success with 3D printing.
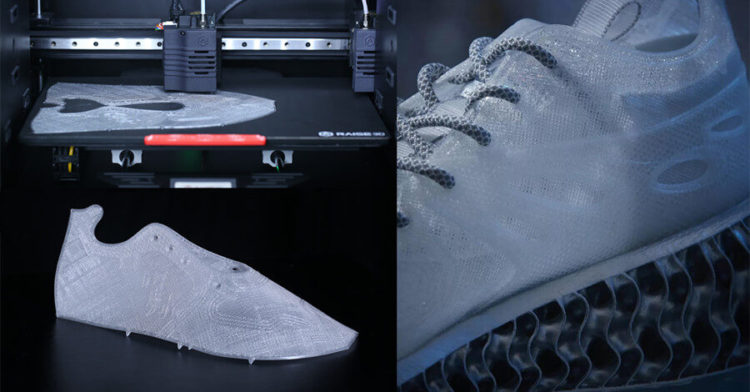
Sneaker with a 3D-printed shoe upper, launched in 2020
Traditional Shoe Production Has High Costs
In the complete sneaker production process, the production of shoe uppers requires a large investment of assets and time. The mainstream shoe upper manufacturing process is called flat knitting, with Nike’s Flyknit and Adidas’s Primeknit being leading examples of this technique. The knitting machine required to process flat knitting is an automated, cost-intensive piece of large-scale equipment. A shoe factory needs to rely on large batch-production with this kind of expensive equipment to survive in the market. This means deploying dozens, even hundreds of knitting machines, around the clock and every day, to produce shoe uppers. Even then, a larger number of workers are required to finish the post-processing, which includes ironing and cutting. On average, one machine needs at least two workers.
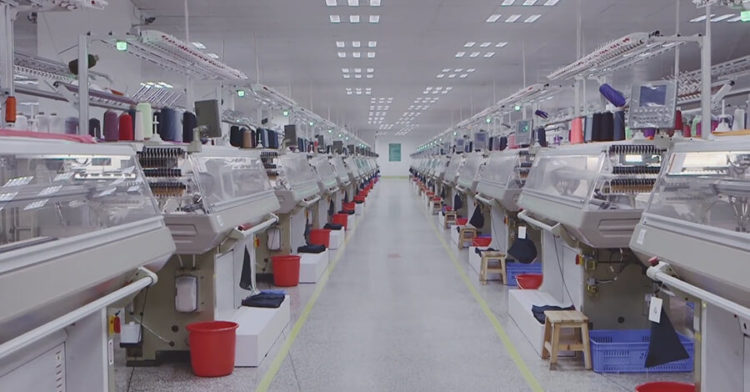
HYPEBEAST. (Jan 30, 2015) Process: The Adidas Ultra Boost AKA „The World’s Best Running Shoe“. Youtube. Retrieved from https://youtu.be/4J_kxwT9zX4
Although the knitting machine can operate automatically, its output still requires a great deal of post-processing. The knitting machine is fed with polyester fibers and fabricates all shoe uppers in one warping sheet. Labor-intensive ironing and cutting will follow to deliver flat and ready-to-go uppers. If the shoe upper is designed with a non-knitting pattern on the surface, then additional steps are needed in post-processing. For example, stitching and gluing is necessary to adhere the material, such as leather or plastic, to the shoe upper.
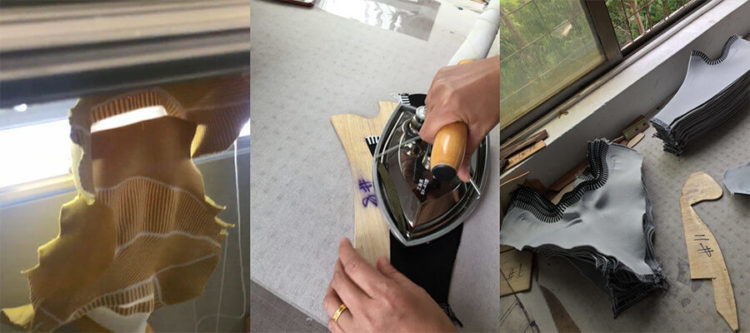
Source 1. long xing. (May 10, 2019) HIGH-PERFORMANCE 3 SYSTEM FLYKNITTING SHOE UPPER MACHINE. Youtube. Retrieved from https://youtu.be/QuQ3zK1MNjU; Source 2. https://www.sneakerfactory.net/
Changing Trends Make it Harder to be Profitable
On average, a new product’s complete R&D cycle needs a minimum of 18 months. Most of this R&D cycle focuses on shoe upper prototyping, using the conventional knitting process. However, consumer preferences of sneaker fashion change every 3 years, and change of taste will only become faster in the future. This generally means that the profitable time-span for each new product is less than a year and a half. Since the window of a product’s profitable time-span is getting smaller, so is the total return on investment.
Incorporating Additive Manufacturing with Raise3D
Raise3D has developed an innovative FFF (Fused Filament Fabrication) shoe upper manufacturing process which is computerizable and fully automated. In this process, a flexible 3D printer filament, TPU (Thermoplastic Polyurethane), is continuously fed into a 3D printer. The threads of TPU filament are extruded as threads on a flat bed. Similar to knitting a woven textile, the TPU threads follow a predetermined design. The TPU filament threads are deposited across each other and adhere to one another following the programmed instructions fed to the 3D printer. Unlike the knitting process, 3D printing immediately delivers a complete shoe upper with all patterns already applied.
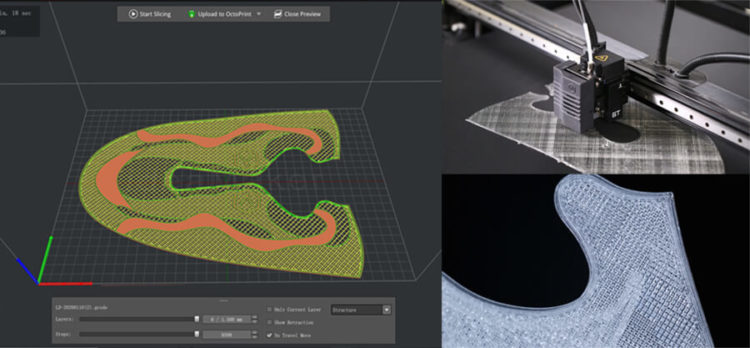
Raise3D’s digital process of shoe upper manufacturing
Raise3D’s solution is a digitalized process where almost all of the fabrication parameters are defined by a single 3D slicing program, ideaMaker. By working with a single piece of software, the manufacturing process is more efficient than having to calibrate the process to accommodate many types of hardware and raw material. Furthermore, Raise3D also provides RaiseCloud, a cloud-based 3D printing management software to seamlessly and wirelessly connect with Raise3D printers to make remote batch printing management a lot easier. RaiseCloud’s management capabilities include a printing progress overview, live monitoring, print job order assignment, printer control, file sharing, and team communication. The combination of hardware and software in Raise3D’s ecosystem helped factories digitalize the shoe upper manufacturing process from both a management and fabrication perspective.
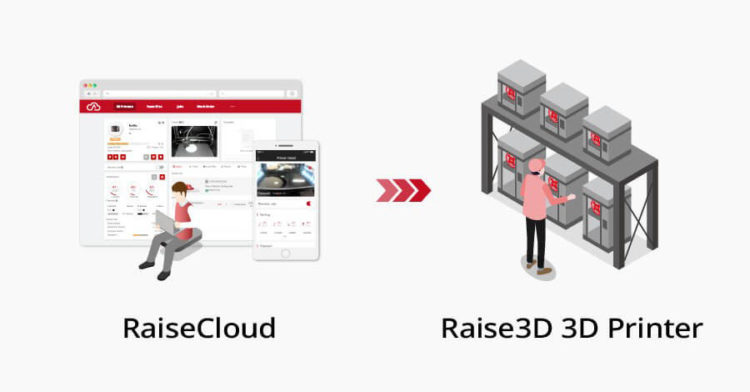
RaiseCloud allows user to remotely manage multiple printers from one computer
3D Printing Improved Prototyping
Using 3D printing with Raise3D for a new product’s R&D cycle has a timeline of 3 months, which is especially short when compared to the previous R&D cycle of 18 months. Each new product has multiple shoe upper designs that need to be evaluated before the best design is selected. Each design is repeatedly adjusted and abundantly sampled. With Raise3D’s process, producing a sample of a new shoe upper does not require adjustment tools or sophisticated programming. By simply importing the digital design file and customizing a few settings within the software, 3D printers can quickly begin to produce the new samples.
3D printing shoe uppers with Raise3D also enables the shoe upper to be printed with designed texture, outline and decorative patterns on the shoe’s surface in a single print job. Due to the flexibility of Raise3D technology, the shoe’s visual appearance can work in parallel with the wearing experience of the shoe upper. For example, a shoe upper might be tighter or more elastic. This duality will save numerous additional production procedures such as cutting, stitching and gluing. This means the prototyping process will be shorter since it eliminates the verification needed for mass-production feasibility.
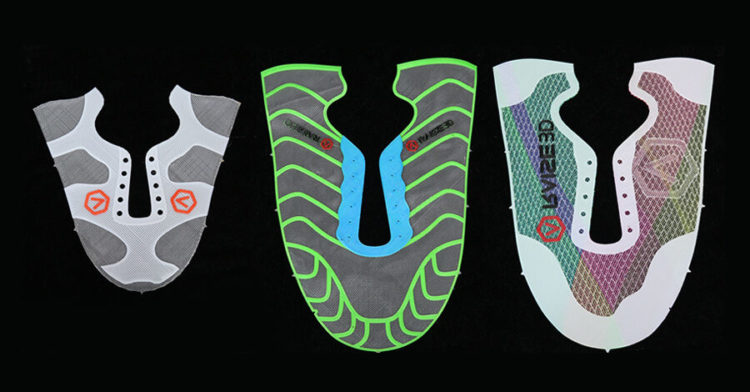
Samples of shoe upper using Raise3D’s technology
3D Printing excels at Small Batch Manufacturing
All shoe manufacturers need a small batch of new products for pilot launches at trade shows. In Raise3D’s case, the factory was able to easily organize a small batch production without cost-shifting or expenditure on extra material procurement. Some features of 3D printers from Raise3D include, but are not limited to, the machine’s small size, its ability to work independently, and enormous flexibility. The factory was able to quickly produce new shoe uppers in a range of designs using industrial 3D printers from Raise3D. These printers ran automatically around the clock to complete shoe uppers for the pilot launch.
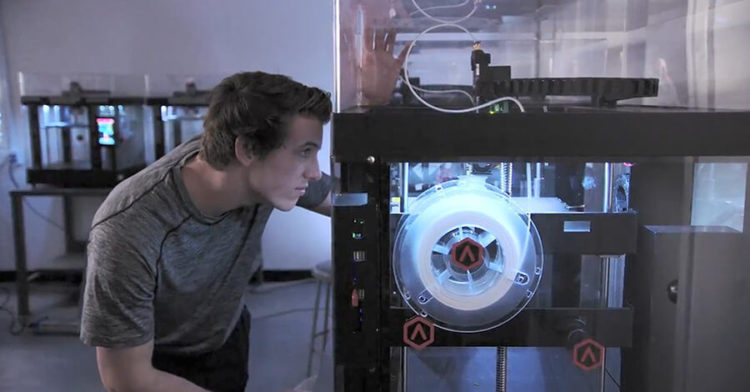
Raise3D’s FFF printers are small and flexible
The Future of 3D Printing
Years ago, before manufacturers began producing 3D-printed shoe uppers, some sneaker manufacturers produced 3D-printed mid-soles and insoles. Since 3D printing changed the process of sneaker manufacturing to accommodate changing business needs and trends, 3D printing has carved out its place and is definitely here for the long-term. Raise3D has built a 3D printing ecosystem to help businesses and industries adopt additive manufacturing. This 3D printing ecosystem gave sneaker manufacturers the ability to adapt, meet demand for customization and made small batch production feasible, all of which is becoming more mainstream.