Team Dynamics is a leading company in the automotive parts industry, based in Droitwich, Worcestershire, UK, and specializes in providing bespoke race-winning solutions to racing teams, drivers and customers all around the world. They focus on building, preparing, maintaining and running vehicles for their customers, giving everyone the opportunity to enjoy all the knowledge and technical capabilities of Team Dynamics and put this into their cars competing in the BTCC (British Touring Car Championship).
Challenges Faced by Team Dynamics in the Past
When it comes to consumer-level industries that focus on producing large quantities of parts at a low cost, the current additive manufacturing (AM) process is often considered able to meet those needs. James, the team’s technical director, said that before they used 3D printing, most things were done overnight and the process would take several consecutive weeks and at a massive cost. Tom, the designer’s team leader, responded by initially seeking out 3D companies to help them make car parts, but as the demand grew for each season, they opted to buy their own 3D equipment to print on, and from there, they chose Raise3D’s Pro2 Plus.
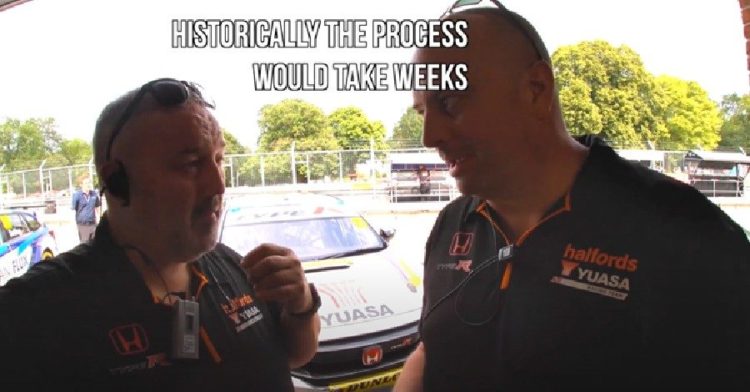
Before they opted for 3D printing technology, they faced significant time and money costs
Large Build Volume Inspires Higher Productivity
After purchasing the Raise3D Pro2 Plus, Dynamics Racing has printed many parts for their Honda Type R BTTC, including air intakes, bonnet louvres, break duct blanks, supports, turning vanes and much more.
With a build volume of 305 x 305 x 605 mm, the large build volume of the Raise3D Pro2 Plus’s confers greater malleability on the produced part. By utilizing a wide range of build volumes, Team Dynamics was able to print bonnet louvers and air intakes with a good surface finish all in one go. This allows them to print entire large pieces rather than connecting smaller pieces. Tom said, „the printer is in operation 24 hours a day and it’s never idle“.
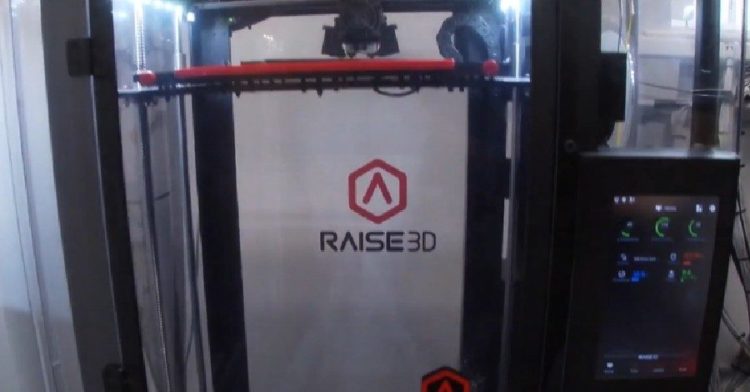
Raise3D Pro2 Plus’s dimensions: 305 x 305 x 605 mm
3D Technology Saves Time and Cost
Historically, it took Team Dynamics several weeks to produce a prototype. In contrast, now the entire production process takes only a few days. Generally speaking, molds can be one of the most time consuming and expensive components of the production process as each iteration is very expensive. The use of 3D printing has saved them around £2,000, according to James. To a large extent, Raise3D meets Team Dynamics’s need to save time and labor costs, and thus improve production efficiency.
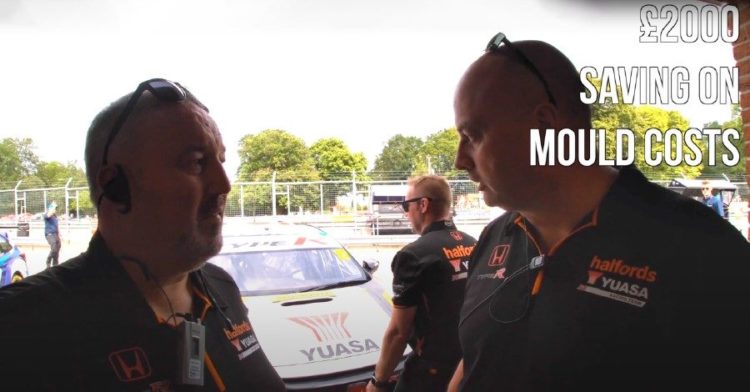
3D printing saves time and money for the Team Dynamics
Seek for Endless Material Possibilities
„Enable us to change and shape things differently“–James Rodgers, team manger of Team Dynamics
Currently the Team Dynamics chooses to use PLA as its main material to print car parts, but in the face of the different needs of different customers, it is necessary to choose different materials and different printing parameters to manufacture the corresponding parts. Compared to traditional manufacturing processes, 3D technology gives you greater design freedom, as it can print nearly any geometric shape, which allows developers to change the design according to the individual needs of customers. At this point, the Pro2 Plus can fully meet demand. Tom said Raise3D was able to help them explore new materials and get more printing parameters. In addition, James said, „it’s different, it has moved us forward“.
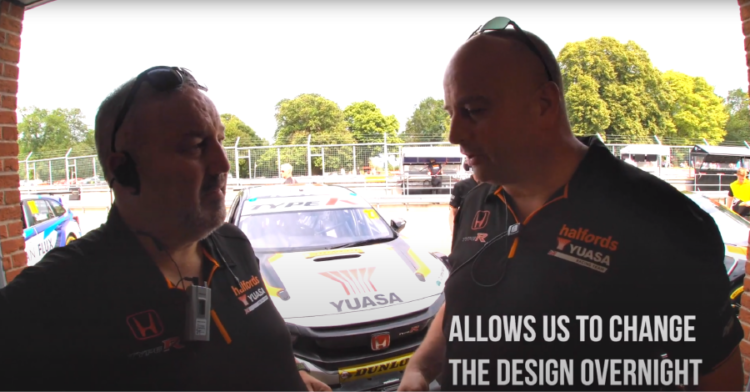
The availability of more materials gives them more possibilities to shape parts
Current Status Quo of 3D Printing in the Automotive Industry
3D printing technology is now being used in a wide range of automotive manufacturing applications. From the interior parts of cars to tires, front grilles, engine blocks, cylinder heads, and air ducts, 3D printing technology can create prototypes of almost all automotive parts. Not only that, but in any manufacturing industry that requires mass production to achieve sufficient productivity, it is crucial to choose the most efficient means of production, and 3D printing technology is certainly the best choice.
This case study was provided by 3DGBIRE, the Raise3D sales partner in UK.
Learn more about the application of Raise3D in automobile parts: https://www.raise3d.com/case/5-times-faster-cost-reduced-by-90-3d-printing-benefits-prototype-design-of-automobile-parts