LutraCAD B.V. is based in Heeswijk-Dinther in the Netherlands, and provides specialized software solutions for orthopaedics and podiatrists in over 104 countries. By merging advanced technology with healthcare needs, LutraCAD aims to help practitioners simplify and automate the production of custom insoles, shoe lasts, midsoles, test shoes, and braces.
Their co-founder and CEO, Niels den Otter, explains that LutraCAD primarily uses the Raise3D E2 printer, specifically chosen for how efficiently it can produce insoles. Additionally, their own customers in the healthcare sector, also prefer Raise3D as a solution, employing Raise3D printers for various printing needs.
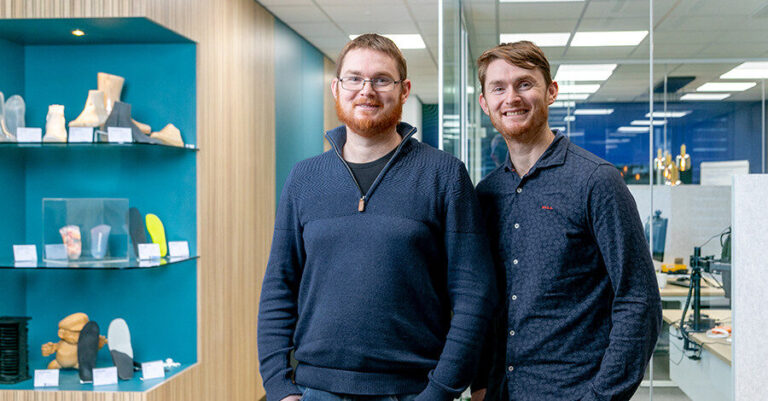
Jordy and Niels, founders of LutraCad
The Challenges of Traditional Production
Traditionally, podiatrists crafted insoles either manually or with milling machines, typically utilizing blocks of EVA or Polypropylene. However, this process generates substantial dust, noise, and requires significant time and investment. Moreover, it has a significant environmental impact.
Additionally, using traditional raw material means having a large quantity of it in stock. Conversely, the filament needed for 3D printing requires much less storage space, meaning less stock, so the value of the material you have to keep in stock is also lower. And that can be reinvested in the company.

3D printing facilitates the simplified and automated production of custom insoles, shoe lasts, midsoles, test shoes, and braces
Why Go for A Modern Production Technology?
3D printing offers a more efficient, cost-effective, and environmentally friendly alternative. By adopting the Raise3D E2 printer, LutraCAD was able to streamline the production process, reduce waste, and create a cleaner working environment. The insoles can be produced in a matter of hours, with time savings of around 50%.
In addition to its affordability and user-friendly features, the printer boasts a closed-box design with a HEPA filter, ensuring the safety of those who use it.
Transitioning to 3D printing eliminates the need for extensive post-processing, significantly reducing labour time and costs. Moreover, it minimizes the dependency on specialized knowledge for sanding and shaping insoles, making it accessible to a broader range of practitioners.
Looking ahead, LutraCAD aims to continue enhancing efficiency and precision in practitioners’ work.
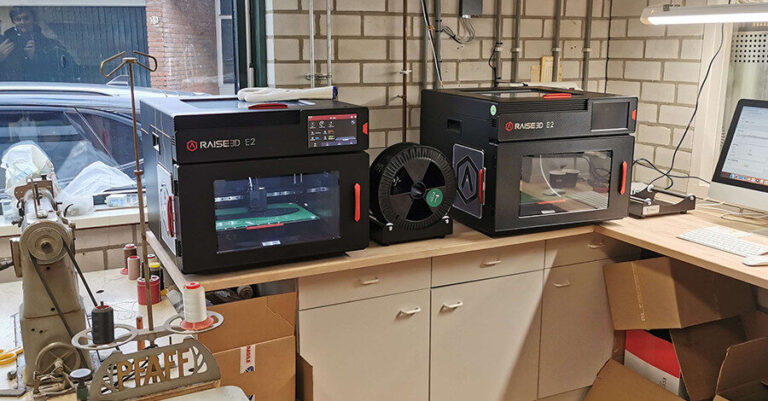
Raise3D’s E2 3D printers are the preferred choice for in-house production of custom insoles
Finding the Right Partner
“We were investigating the best solution to print TPU,” Niels says. “All the reviews on the internet led us to Raise3D as the best TPU printer available on the market.” TPU is a common choice of printing material, as is Polypropylene (PP), and in the case of insoles, their properties are much appreciated.
“TPU for insoles because this is flexible and soft,” Niels affirms. “Polypropylene because people need to be able to stand on a print of just about 3 mm thick and should not break. It is wear-resistant, and the layer adhesion is great.”
He goes on to describe the fruitful relationship between LutraCAD and Raise3D. “After our research, it must have been a coincidence, Raise3D reached out to us to form a partnership. Now it has been 3 years since our first contact.”

Combining LutraCad’s advanced technology with Raise3D 3D printing solutions facilitates the efficient, clean, and precise production of custom insoles
Raise3D Solution
3D printing is revolutionizing manufacturing with its efficiency, cost-effectiveness, and environmental benefits. LutraCAD’s use of the Raise3D E2 printer has streamlined production, reduced waste, and improved workplace safety.
- Streamlined Production and Cost Savings: The Raise3D E2 printer produces insoles in hours. This rapid process reduces labour and post-processing costs, making 3D printing a highly cost-effective solution.
- Environmental and Safety Benefits: 3D printing generates minimal waste, supporting LutraCAD’s sustainability goals. The printer’s closed-box design with a HEPA filter ensures a safe, clean working environment.
- Accessibility and Reduced Need for Specialized Knowledge: The user-friendly printer design eliminates the need for specialized skills in sanding and shaping, making the technology accessible to more practitioners.
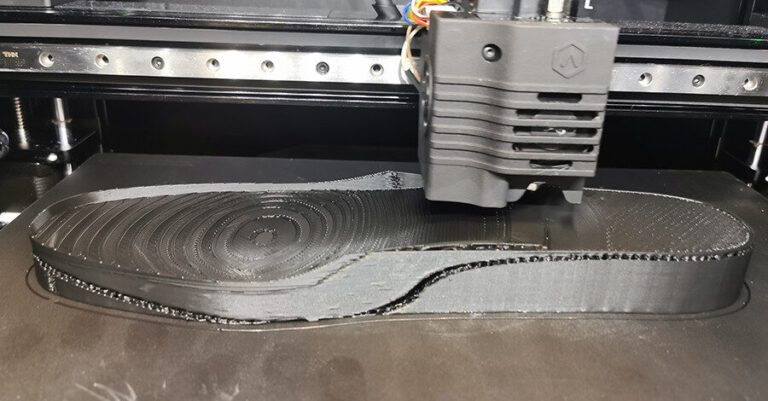
Midsoles are being 3D printed using a Raise3D E2 printer
LutraCAD’s plans are to leverage ongoing advancements in 3D printing to further enhance efficiency and product quality, staying at the forefront of technological innovation.
In summary, 3D printing offers significant advantages, transforming manufacturing processes and setting the stage for future innovations.
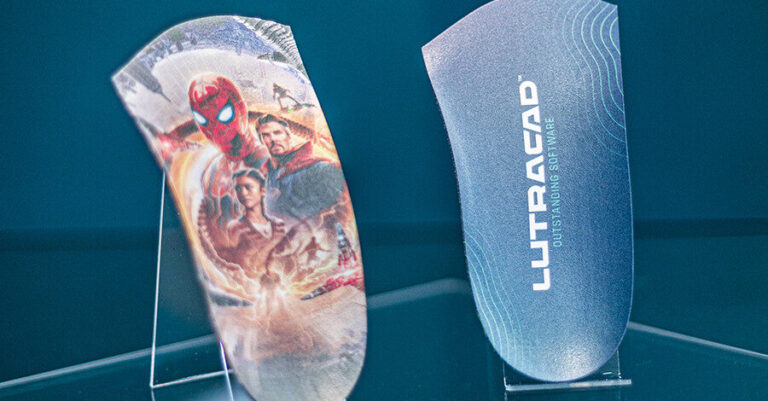
Besides being durable, flexible, and impact-resistant, 3D-printed insoles can also be customized to customer’s preferences
What LutraCAD Added to the Table
LutraCAD has significantly enhanced the insole manufacturing process by providing an end-to-end solution that streamlines production from design to final product. Key innovations introduced by LutraCAD include:
- Automatic Slicing for 3D Printing Files: LutraCAD’s software automates the slicing of 3D models, optimizing them for printing. This eliminates the manual process of preparing files, reducing errors and saving time.
- Integrated 3D Printer Network: The software allows for seamless integration with 3D printers, enabling direct file transfer over the network. This feature simplifies the workflow, making it easier and quicker to start printing jobs.
- Research-Driven Printing Methods: LutraCAD has invested in extensive research to determine the best printing methods for insoles. This includes identifying the ideal nozzle size, using a glass print bed for better adhesion and finish, and conducting durability tests to ensure the printed insoles meet high standards of wear and performance.
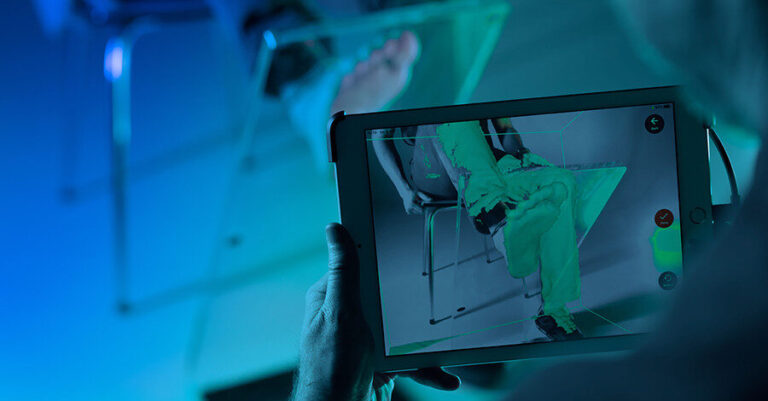
LutraCAD’s software streamlines and automates the insole pre-production process.
By combining these advanced features, LutraCAD not only improves the efficiency and quality of insole production but also reduces the overall cost and complexity of the manufacturing process. This makes high-quality, custom insoles more accessible to practitioners and ultimately benefits the end-users who rely on these essential medical devices.
Conclusion
LutraCAD’s innovative solutions, in partnership with Raise3D, are transforming the way insoles are manufactured, providing a more efficient, cost-effective, and environmentally friendly alternative to traditional methods. By leveraging advanced 3D printing technology and integrating it seamlessly into the production workflow, LutraCAD and Raise3D are setting new standards in the orthopaedic and podiatry industry.
Start 3D Printing Custom Orthotic Insoles Right Away
We now offer a 3D Printed Insole Solution Trial Bundle and a Production Bundle in Europe. You can learn more about our bundles and the insole printing process on our 3D Printed Insoles page.